В предыдущем материале было описано производство катаной брони для танков «Тигр», «Пантера» и «Тигр 2», а также её особенности и анализ — теперь попробуем разобраться с производством изделий. Производство немецких танков в годы Второй мировой войны было организовано таким образом, что заводы-сборщики получали все комплектующие, а затем осуществляли их полную сборку. Одним из важнейших типов комплектующих являлись бронекорпуса и бронебашни. Сегодня разбираемся с нюансами их производства.
Основные тенденции
Начать следует с конструкций корпусов и башен, поскольку в ходе разработки новых машин были применены новые для немецкого танкостроения технологии.
Для корпуса танка Tiger Ausf. E в основной массе использовались классические для немецких танков того периода соединения в замок с механической обработкой кромок. Однако, увеличение толщины бронелистов и воспринимаемой ими нагрузок привело к тому, что часть деталей стала собираться с помощью врезного шипа. С помощью врезного шипа соединялись: нижний лобовой лист с бортами корпуса; наклонный лобовой лист с бортами корпуса, а также кормовые листы с бортами корпуса.
В соединении использовались полукруглые заглушки для уплотнения со стороны торцов шипа. Отдельно стоит отметить усиление соединения борта корпуса с днищем подкрылка с помощью угольника. К днищу подкрылка угольник крепился заклёпками, к борту корпуса — болтами. Дополнительно, всё соединение было усилено 6-мм уплотняющим швом. Все кромки фрезерованы или строганы на станках. На ряде деталей применена газовая резка, так, например, на наклонном лобовом листе корпуса прямые кромки вырезаны газом на автоматах, а профилированный рез — с помощью ручной газовой резки.
Несмотря на механическую обработку кромок, при осмотре подбитых танков было выявлено, что зазоры между деталями доходят до 10 мм. При этом технологические прокладки не использовались.До весны 1942 года при изготовлении броневых деталей корпуса и башни применялась разделка листов на металлорежущих станках, однако стараниями главы танкового производственного комитета была реализована идея использования газовой резки. Она должна была применяться для изготовления броневых деталей, соединявшихся между собой с помощью сварных шиповых соединений, в то время как для соединений внахлёст или в замок по-прежнему применялась машинная резка. Изготовление бронелистов с помощью газовой резки очень выгодно отличалось от машинной обработки своей экономичностью.
После поступления с завода-производителя бронелисты разрезались секаторами на прямоугольные заготовки для последующей резки деталей. Непосредственная резка выполнялась газорезательными автоматами с магнитным ведущим роликом. Высокое качество реза поверхности обуславливалось использованием ацителено-кислородного пламени при высокой чистоте кислорода. Широко использовалась резка с одновременным снятием фасок, когда одновременно работало несколько горелок. Если кромка вырезанной детали должна была проходить последующую механическую обработку, то для уменьшения твердости ее подвергали отпуску. Отдельные поверхности вырезанной детали подвергались механической обработке. Перед газорезкой окалину с металла удаляли с помощью молотка, после чего следовала обработка броневого листа с помощью пескоструйного аппарата. Другие типы очистки и шлифовку не применяли.
Контроль качества поверхности перед сварочными работами практически отсутствовал. В директивах завода F. Krupp на сварку брони было указано, что «обязательным условием является добросовестное качество изготовления всех деталей». При осмотре боевых машин в различных цехах F. Krupp и Dortmund-Hoerder Huttenverein (далее DHHV) в 1945г. не было выявлено ни одного случая, который бы доказывал, что предпринимались попытки отшлифовать или удалить окалину с листов, расположенных рядом со сварными швами.
При производстве немецких танков широко применялась гибка бронелистов всех толщин после окончательного их обрезания. Листы толщиной более 50 мм нагревались до 300°С, а толщиной менее 50 мм — до 150–200°С. При нагревании использовался бытовой газ, оно проводилось непосредственно перед размещением листа под прессом. Допуски на плоскостность составляли 5 мм, однако там, где длина листа позволяла согнуть его тисками, чтобы установить правильные зазоры между свариваемыми кромками, допускалось большее предельное отклонение, чем обусловленное техническими условиями. Гибка 80-мм листов производилась прессом с усилием 2000 тонн с допуском ±2 мм на смещение центра гибки от основной линии.
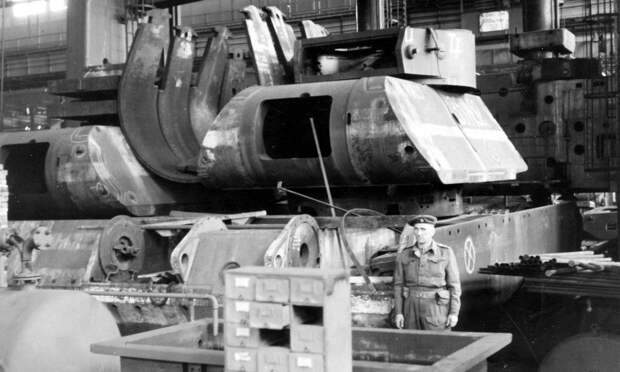
(https://www.tankmuseum.org)
Значительным изменением в производстве бронекорпусов и бронебашен стало широкое внедрение соединения броневых листов в шип. Первым документом в котором упоминается применение такого способа соединения броневых плит в производстве танков являются ТУ T.L. 21/9017, составленные в августе 1942 года. Основной целью внедрения такого типа соединения бронелистов являлось повышение баллистической защиты конструкции за счёт разгрузки сварных швов от опасных напряжений среза. В частности, при допросе представителя фирмы F. Krupp некоего доктора Лукке были указаны следующие причины:
а) шиповое соединение обеспечивало дополнительную баллистическую стойкость благодаря взаимной непосредственной опоре вдобавок к тому, что обеспечивали сварные швы;
б) оно обеспечивало превосходную прочность при увеличении общей длины сварных швов;
в) соединения состояли из небольших отрезков сварных швов, что препятствовало распространению трещин.
Всё вышеперечисленные изменения были использованы при разработке и производстве танка Panther Ausf. D. Практически все основные бронедетали корпуса были соединены в шип. Для сборки башни соединение с помощью врезного шипа использовалось только для сварки бортов с кормовым листом. Литая лобовая деталь башни соединялась с бортами с помощью «ласточкиного хвоста». При осмотре корпусов Panther Ausf. D было выявлено, что зазоры между деталями гораздо меньше, чем у Tiger Ausf. E и допуск на точность реза составлял 1–2 мм.
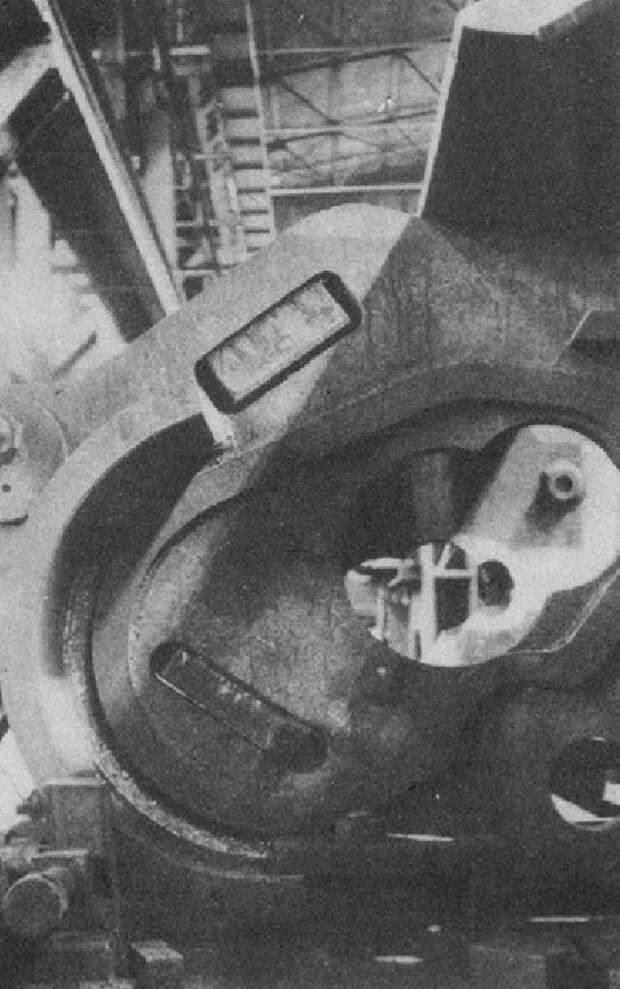
Следующая модификация Panther Ausf. A привнесла ряд изменений в соединения деталей башни и корпуса. Вместо «ласточкиного хвоста» лобовая деталь башни стала соединяться с бортами в шип. А в ходе производства шиповые соединения наклонных листов подкрылка с крышей корпуса, а также бортов корпуса с днищем, были заменены на соединения «в замок».
В результате разработки танков Panther II и VK 45.03, превратившегося в итоге в Tiger Ausf. B, были сформированы окончательные тенденции устройства бронекорпусов для немецкого танкостроения. Были устранены достаточно сложные карманы под топливные баки и систему охлаждения, вместо этого днище подкрылка стало прямым и располагалось под углом относительно продольной оси танка. Шиповое соединение стало использоваться для тех деталей, которые подвергались наибольшей нагрузке при обстрелах.
В шип соединялись лобовые детали корпуса между собой и с бортами корпуса и подкрылка, с бортами и с подкрылком с помощью врезного шипа соединялся и кормовой лист корпуса. Днище подкрылка, днище корпуса и крыша корпуса со всеми деталями соединялись в замок. Такое устройство корпуса использовалось на Tiger Ausf. B, к такому же виду привели корпус танка Panther Ausf. G (с перераспределением толщин бронелистов) и самоходных установок «Ягдтигр» и «Ягдпантера». Башня танка Tiger Ausf B собиралась в шип, кроме крыши башни. Лобовая деталь башни устанавливалась через соединение «ласточкин хвост» и всё соединение дополнительно усиливалось шпонками.
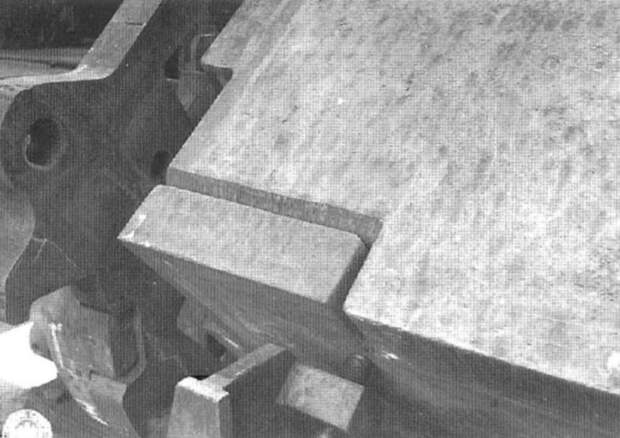
Следует отметить, что корпуса и башни различных производителей могли отличаться, так у танков Tiger Ausf. E и Tiger Ausf. B на башнях F. Krupp и DHHV отличалась разделка под швы, соединяющие крышу башни с бортами, на корпусах танков Panther Ausf. D от фирмы Ruhrstahl резка под шиповое соединение наклонного листа подкрылка и «кармана» выполнялась отлично от других фирм. На F. Krupp не устанавливалась шаровая установка пулемета в верхний лобовой лист корпуса танка Tiger Ausf. B — деталь устанавливали на заводе сборщике Henschel & Sohn, куда она поставлялась фирмой Luftfahrtgeratebau Arno Mueller, Лейпциг.
На осмотренных советскими специалистами корпусах Panther Ausf. D отмечалась высокая точность подгонки деталей корпуса с минимальными зазорами. Только в одном случае была обнаружена технологическая прокладка. Очевидно, к концу войны ситуация поменялась и после осмотра сборочных линий заводов F. Krupp и Dortmund-Hoerder Huttenverein, было отмечено большое количество несоответствий ТУ при сборке шипованных соединений. Избыточные допуски при резке приводили к тому, что технические прокладки в соединениях были не закреплены. Низкое качество сборки основных бронелистов в последствие отрицательно сказывалось на баллистической защите корпусов и башен.
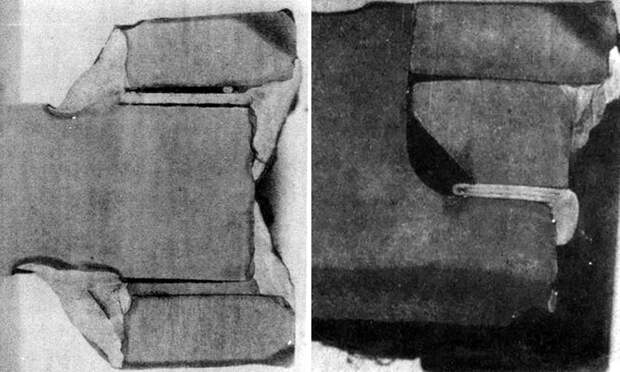
В отличие от танковой промышленности СССР и США, в немецком танкостроении использовалась только ручная сварка. В технических условиях (T.L.4014, 4028 и 4032), озаглавленных «Временные технические условия на броневые конструкции со стенками толщиной 16-30 мм, 35-50 мм и 55-80 мм соответственно» были сформулированы требования к проведению сварочных работ:
1. Следует использовать дуговую сварку металлическим электродом, если иное не предусмотрено чертежами;
2. Перед началом производства Wa Prüf 6 должен представить метод сварки в письменный форме и утвердить его. Все изменения должны пройти повторное утверждение;
3. Включить в процесс сварки рассмотренный перечень показателей:
- тип соединения;
- материал и диаметр электродов;
- последовательность проходов;
- методы снятия структурных напряжений;
- род и полярность постоянного тока;
- сила тока в амперах;
4. В механически обработанных сварных швах не допускаются трещины;
5. Не требуется проводить баллистическое испытание сварных конструкций.
Сварка
С 1942 года и до начала 1944 на производстве немцами использовались аустенитные электроды, электроды для твёрдой наплавки были запрещены к использованию. С начала 1944 года производство по большей части перешло на ферритные электроды. По данным заводов F. Krupp и DHHV вплоть до 1944 года существовала небольшая проблема, связанная с образованием трещин в сварных швах при использовании 18/8 аустенитных электродов. Однако в DHHV при изучении технологических карт на корпус и башню за 1943 год эти данные не были подтверждены. Значительная часть времени, отведённого на сварку, тратилась на устранение дефектов сварных швов.
Обе фирмы, однако, утверждали, что при внедрении ферритных электродов в январе 1944 года проблема образования трещин изрядно усугубилась. На заводе F. Krupp не смогли использовать ферритные электроды в производстве корпусов Tiger Ausf. B из-за образования трещин в сварных швах и на стыках, но без особых проблем в этом отношении применяли их на башнях этого танка.
Представители завода DHHV утверждали, что у них частота образования трещин приближалась к 30-40% и была снижена до 10-20% благодаря усовершенствованию электродов и разработке различных методик. В одной из таких методик предлагалось протягивать исходные швы ферритным и рабочим слоями аустенитными электродами, «потому что более жесткий рабочий аустенитный слой давал хорошие баллистические результаты». Однако весьма вероятно, что это делалось для сокрытия трещин под нижним ферритным слоем. Во время осмотра корпусов и башен в DHHV на стыках аустенитных швов были обнаружены длинные трещины.
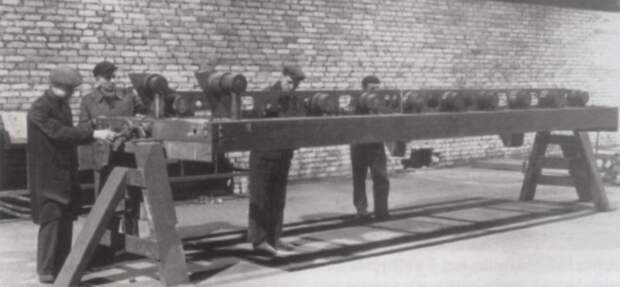
Контроль качества сварных соединений осуществлялся только путем визуального осмотра. Проверялись размеры шва и наличие трещин в шве и зонах термического влияния. При обнаружении трещин длиной более 100мм участок шва должен был быть выплавлен, после чего заваривался. Трещины в металле корпуса в районе швов вышлифовывались, заваривались и снова зашлифовывались.
На DHHV была найдена служебная записная книжка инспектора Магдефрау значительная часть которой посвящена окончательному осмотру корпусов и башен «Пантер» перед их отправкой в начале 1943 года. Упоминаний о трещинах в сварных швах было мало, но, что касается корпусов и башен, то приблизительно в 50% случаев внимание обращалось на тот факт, что крыши и днища выступали на 5-8 мм, а в одном случае — на 10 мм. В записях за июнь 1944 года упомянуты только трещины в сварных швах с указанием их длины, толщины листа и способа ремонта. Большая часть трещин была меньше 100 мм длиной, а некоторые были размером до 400 мм.
Производство
Производство корпусов и башен «Тигров» велось на предприятиях «Круппа» в Эссене и DHHV в Дортмунде. Эти же предприятия позднее перешли на производство корпусов и башен для «Тигров 2», к ним добавилась «Шкода». Производством для «Пантер» занимались «Харкорт-Айккен Эдельштальверке» (Harkort-Eicken Edelstahlwerke GmbH) в Хагене, «Бёлер и Ко» (Böhler & Co) в Капфенберге и Кроттендорф-Гайсфельде (Австрия), DHHV в Дортмунде, Eisenwerke Oberdonau GmbH в Линце (Австрия), «Миттельдойч Штальверке» (Mitteldeutsche Stahlwerke AG) в Кирхмёзере, «Руршталь» (Ruhrstahl AG) в Хаттингене, «Банкхютте» (Bankhütte), он же «Хута-Банкова» (Huta Bankowa) в городе Домброва-Гурнича (Верхняя Силезия).
Наиболее полно описаны процессы сборки корпусов и башен «Пантер» Ausf. G и «Тигров 2» на заводах «Круппа» и DHHV. В целом процесс сборки обоих танков происходил одинаково, за исключением отдельных моментов, обусловленных особенностями конструкцией. Ниже описана сборка корпуса и башни «Тигра 2».
Выделяемое для предварительного отреза всех бронелистов танка Tiger Ausf. B время составляло 40 часов, для окончательного — 53 часа(для Panther Ausf. G — 20 и 40 часов соответственно). На нижней кромке подкрылков сразу делались вырезы, необходимых для последующего рассверливания отверстий под установку задних гидроамортизаторов.
На заводе F.Krupp линии сборки корпусов и башен были поточного типа. После сборки с помощью прихваточных швов на неподвижном стенде, корпус или башня перемещался на одну из четырех линий с шестью подвижными кантователями в каждой, на которых производилось дальнейшее передвижение по цеху с проведением необходимых сварочных работ. Отличие производственной линии на DHHV заключалось в том, что кантователи были неподвижными.
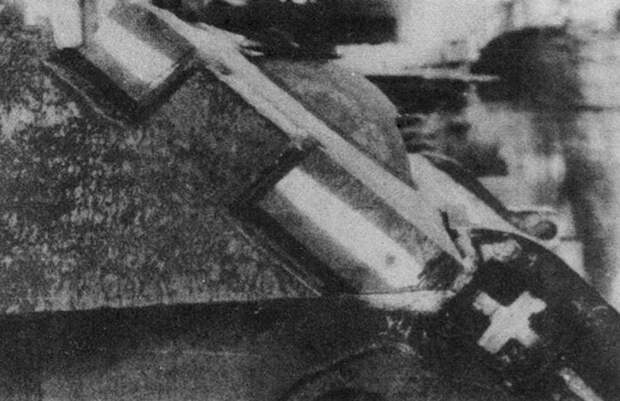
Сборка корпусов и башен на стендах с помощью прихваточных швов являлась предварительным сборочным этапом. Устанавливались все бронелисты за исключением крыши корпуса. Длина прихваточных швов составляла 100-150 мм. Интересно отметить, что на DHHV прихваточные швы выполнялись слесарями-монтажниками, сварщики к этой работе не допускались. До сборки основных листов корпуса осуществлялась сборка силового набора на внутренней стороне днища корпуса, которая проводилась по-разному на F. Krupp и DHHV.
Силовой набор состоял из поперечных и продольных элементов, изготовленных из конструкционной стали толщиной 10 мм. Высота продольных элементов составляла 215 мм, поперечных — 145 мм. К продольным элементам приваривались с двух сторон опорные части торсионов. В поперечных элементах сделаны пазы для стыковки с продольными частями силового набора и отверстия для уменьшения массы. Фиксация поперечных элементов на заводе F. Krupp производилась после сборки корпуса с помощью стыковых накладок. На DHHV поперечные элементы фиксировались с помощью уголков с волнистой кромкой ещё на этапе установки бортовых листов корпуса.
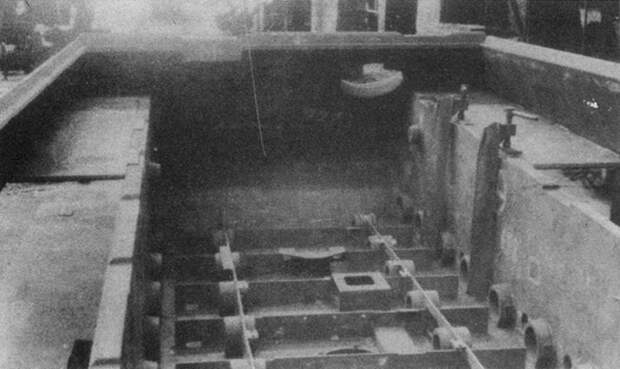
Затем производилась сборка подкрылков и, в последнюю очередь, устанавливался кормовой лист. Установка и позиционирование листов осуществлялись с помощью специальных кронштейнов. Соединение бронелистов сопровождалось установкой технических прокладок. На Tiger Ausf. B было упрощено соединение с помощью врезного шипа. Для него не требовалась установка полукруглых заглушек, вставлялись только технические прокладки (T.L. 21/9017). Сварка корпуса прихваточными швами происходила по следующей схеме:
- Внутри между днищем и бортовыми листами;
- Внутри между днищем подкрылка и бортовыми листами;
- Внутри между днищем подкрылка и подкрылком (только один проход);
- Внутри между днищем и нижним лобовым и кормовым листами;
- Внутри от днища подкрылка до верхнего лобового и кормового листов;
- Снаружи между верхним лобовым листом и подкрылком и бортовым листом. Сварка выполнялась в положении стоя;
- Снаружи между верхним и нижним лобовыми листами;
- Внутри между бортами корпуса и нижним лобовым и кормовым листами. Сварка выполнялась в положении стоя.
Сборка башен начиналась с листов основания, остальные бронелисты устанавливались с помощью кронштейнов и регулировались болтами. В отличие от F.Krupp, на DHHV сборка башни велась в перевёрнутом положении. Внутренние угловые швы выполнялись в вертикальном положении с помощью 18/8 электродов. Швы выполнялись в два этапа: первый проход в корне шва толщиной 5 мм, затем три прохода. На этом этапе крыша башни не устанавливалась.
В отчёте «Welding design & fabrication of german tank hulls & turrets», оставленном английскими специалистами после войны отмечается крайне низкое качество прихваточных швов и большое количество трещин в них.
После предварительной сборки корпусов и башен они помещались на кантователи. Вращение корпусов и башен на кантователях производилось только вокруг продольной оси, что позволило не усложнять конструкцию. Кантователи для сборки корпусов на фирмах F. Krupp и DHHV имели ряд отличий. На кантователях в цехах DHHV для вращения использовался силовой привод с помощью двигателя постоянного тока мощностью 12,5 кВа, в то время как кантователи, установленные на F. Krupp, имели ручной привод.
Задний кронштейн кантователя на заводе F. Krupp имел два болта большого диаметра и шайбы на нижней стороне, а также крючковое приспособление, которое проходило по верхнему краю кормового листа и туго затягивалось третьим болтом. Задний кронштейн у DHHV был прикреплён к кормовому листу корпуса с помощью множества болтов небольшого размера и, соответственно, имел разнообразные ребра для крепления к станине кронштейна, расположенного рядом с этими болтами.
Передний кронштейн на обоих заводах имел сходную конструкцию. Корпус крепился к переднему кронштейну за проушины в бортах, кронштейн упирался в лобовые детали с помощью болтов большого диаметра. Привод располагался перед кронштейном, на который устанавливалась лобовая часть корпуса. Доступ к корпусам, расположенным на кантователях, на фирме F. Krupp обеспечивался с помощью лёгких сварных платформ, сделанных из трубчатых секций. Эти платформы были лёгкими и обеспечивали свободный доступ к корпусу. К корпусам на кантователях в цехах DHHV обеспечивался только с помощью приваренной к кантователю стремянки.
Кантователи для сборки башен также имели различия. В кантователях на заводе F. Krupp использовался прямой шпиндель, к которому крепилась собираемая башня: с одной стороны крепление осуществлялось к кормовому листу, с другой — к амбразуре в лобовом листе. На кантователях в DHHV был сделан поворотный стол, к которому собираемая башня крепилась болтами. Кантователи для сборки башен были неподвижными и на F. Krupp, и на DHHV.
Сварка корпуса Tiger Ausf. B проводилась по следующей схеме:
1. На кантователе вверх днищем
- Снаружи между днищем и бортовым листом;
- Снаружи между днищем подкрылка и кормовым листом;
- Между днищем подкрылка и бортовым листом;
- Снаружи между кормовым листом и бортом корпуса и подкрылком;
- Снаружи между нижним лобовым листом и бортом корпуса;
2. На кантователе, повёрнутом на 90° из положения стоя, сначала слева наверх, затем справа наверх
- Внутри между днищем подкрылка и бортовым листом;
- Внутри между подкрылком и лобовым и кормовым листами.
Направление во время проведения сварочных работ не контролировалось. Исключение составляли только продольные соединения, сварка которых проводилась от середины к краям, и соединения, сварка которых выполнялась в положении стоя, они сваривались в направлении снизу вверх несколькими проходами.
Заключительным этапом сборки корпуса на кантователе являлась установка крыши. Крыша опиралась на поперечный лист, выполненный из качественной конструкционной стали толщиной 20 мм. Опорный лист фиксировался клиньями между бортовых листов корпуса, и с помощью клиньев у днища подкрылка прижимался к крыше корпуса. С помощью клиньев выбирались допуски на внутренние размеры корпуса. Так, например, допуск на расстояние между бортовыми листами корпуса составлял ± 8 мм. Крыша корпуса к опорному листу приваривалась прерывистом швом. Для исключения возможности нанесения непрерывного шва в опорном листе были сделаны 4 выреза по верхней кромке. Ещё два небольших опорных листа устанавливались с каждой стороны посередине боевого отделения. Сама крыша сваривалась из трёх бронелистов.
На полную сварку корпуса отводилось 136 часов.
При сборке башни на кантователе одним из самых ответственных этапов являлась установка крыши. Крыша, состоящая из трех листов, подгонялась индивидуально к каждой башне. Во время подгонки на каждом из трех листов ставились специальные пометки и выполнялась профильная резка, после чего все три листа сваривались в стык и устанавливались на башню, расположенную на кантователе. Сварка башни проводилась по следующей схеме:
Швы между крышей башни и бортами выполнялись и снаружи и изнутри двумя сварщиками в два прохода, начиная от середины и далее по направлению к краям. Для сварки использовались ферритные электроды.
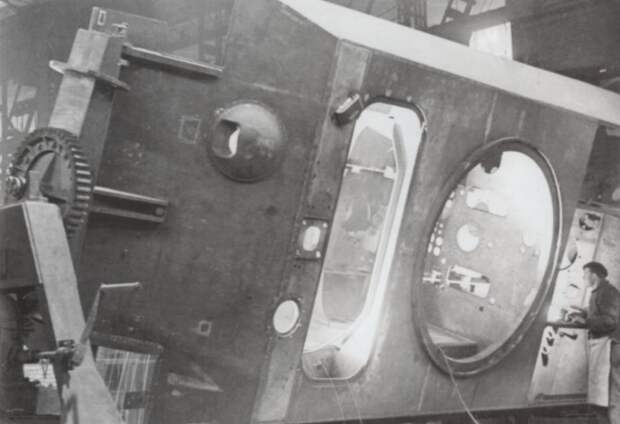
- Аналогичным способом проводилась сварка между листами основания башни и бортами.
- Швы внутри между крышей и кормовым и лобовым листами выполнялись 18/8 аустенитными электродами
- Все наружные швы выполнялись ферритными электродами.
На F.Krupp был внедрен весьма оригинальный способ оплаты труда сварщиков. Согласно словам упомянутого выше доктора Лукке, им платили сдельно на основании массы наплавленного металла. На DHHV оплата была сдельной на основании рабочего времени.
Интересно отметить, что использование прихваточных швов использовалось не на всех заводах. Так, например, на предприятии Mitteldeutsche Stahlwerke AG при сборке корпусов Panther детали предварительно сваривались одноваликовыми швами по всей длине.
Готовые корпуса и башни подвергались осмотру инспекторами из бюро инспекций при управлении вооружений сухопутных войск. Кроме того на обоих предприятиях существовала система цехового контроля. Число одновременно работающих инспекторов в цехах F.Krupp составляло 12–14 человек.
Для сборки корпусов на F.Krupp использовались 4 подвижные линии с 6 кантователями в каждой. Перемещение линии осуществлялось после того как готовый корпус из первого кантователя перемещался на смотровую площадку. Сварочные аппараты представляли собой генераторы постоянного тока. Производительность при работе всех линий составляла от 70 до 120 корпусов в месяц.
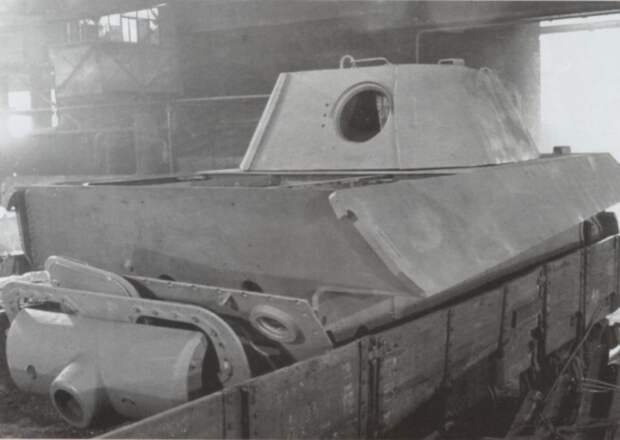
Для сборки корпусов Tiger Ausf. B на DHHV использовалась половина цеха. Вторая половина предназначалась для сборки корпусов Panther. Размеры цеха составляли 300×25 м. Сборочные линии Tiger Ausf. B и Panther были разделены центральным проходом шириной 3 м. В одном конце цеха располагались стенды для сборки подузлов. По бокам цеха располагались 20 неподвижных кантователей для корпусов Tiger Ausf. B и 34 — для Panther Ausf. G, доступ к силовым приводам которых осуществлялся из центрального прохода. Сварочные аппараты были двух типов: первый тип мог использоваться только одним сварщиком, второй был рассчитан на двух. Производительность могла составлять до 45 корпусов Tiger Ausf. B в месяц и до 120 корпусов Panther Ausf. G.
Сборка башен на DHHV проводилась в другом цеху также совместно со сборкой башен Panther. Для сборки башен в цеху, размер которого составлял 126×10 м, имелось 12 кантователей для Tiger Ausf. B и 7 — для Panther Ausf. G.
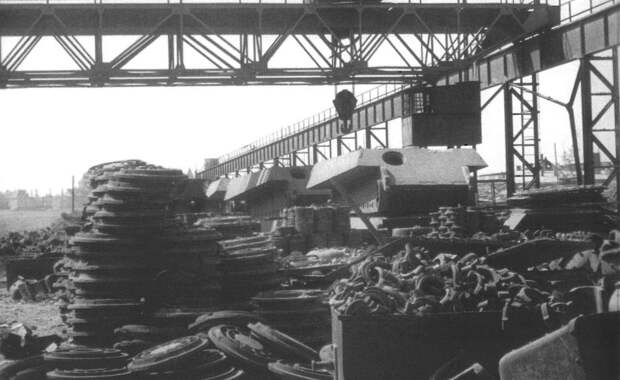
На момент захвата предприятий союзниками на линиях последними значились следующие номера: 462 — для корпуса и 431 — для башни танка Tiger Ausf. B на заводе F. Krupp; 174 — для корпуса и 204 — для башни Tiger Ausf. B, и 1022 — для корпуса, 1597 — для башни танка Panther Ausf. G на заводе DHHV. На корпусах и башнях набивался присвоенный им на производстве серийный номер. Аббревиатура «bwn» использовалась для обозначения производителя F.Krupp, «amp» — DHHV.
В целом для производства бронекорпусов и бронебашен немецких танков «Тигр» (в меньшей степени), «Пантера» и «Тигр 2» можно сделать следующие выводы:
- широко применялись шиповые соединения и газовая резка бронедеталей;
- для сборки использовались кантователи, позволяющие фиксировать корпуса и башни в любом положении;
- использовалась только ручная сварка;
- как и в случае с производством катаной брони, недостаточно хорошо был организован контроль качества, результатом чего стали многочисленные нарушения технических условий и снижение баллистической стойкости корпусов и башен танков.
Источники и литература:
- Материалы ЦАМО РФ
- Материалы Bovington Tank Museum
- Материалы NARA
- Вестник танковой промышленности №9 — Москва: Наркомтрансмаш, 1945